Considering cold storage warehouse construction? The supply chain for perishable goods is rapidly changing due to increasing demand and competition. Production, storage and transportation are a challenge, but modernization has resulted in higher productivity levels and bigger warehouses.
Costs are always a concern for manufacturers and businesses that are always looking for ways to minimize their investments. While there’re plenty of rental options out there, many manufacturers and producers are often interested in setting up their own cold storage warehouses. However, there are costs involved, and they often rise if things aren’t planned out well. To begin, its important to understand the requirements and devise a suitable construction plan, design and budget accordingly.
Let’s review all information that can come in handy when setting up a cold storage warehouse.
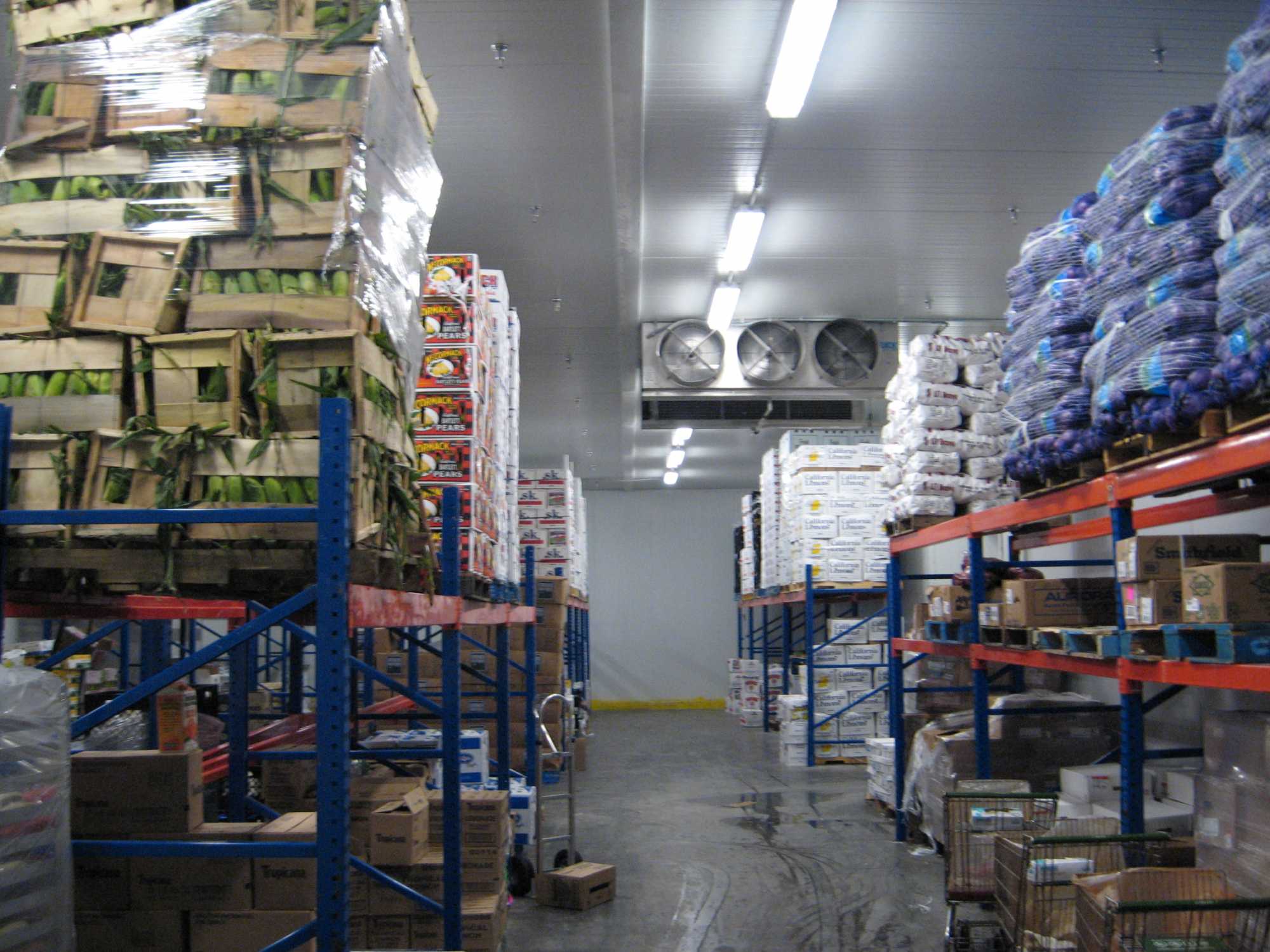
44×317 Brown Supermarket Steel Building located in Pompano Beach, Florida
Reviewing the Design Elements
Several design elements come into play when planning out cold storage construction. All these factors affect performance, and hence, must be the most suitable for application.
Space and Size
Think long term, and figure out your expectations from the project in the next 10 to 15 years. Understand the costs involved and the amount of product that you’ll have to store. Most important is the return on investment that you’ll be able to generate through the completely constructed warehouse.
Decide a suitable facility size, the manner in which the product will be stored, and the way in which you’d be able to access shelves. Decide between pallets and bits, and ponder upon a suitable cooling unit. Also if your warehouse has rooms for different purposes, they must be properly separated. When planning out the design, keep in mind the fact that you may want to expand the warehouse later on.
Food Quality
The design of the space should be such that food quality is maintained throughout phases: processing, packaging and shipping. Location should also be considered; sites near transportation lines are considered to be the most ideal situations, but greater costs are involved.
Energy Consumption
Energy costs associated with cold storage warehouses can reach thousands every month. These can be decreased by installing under-floor heating systems, considering temperatures of adjacent rooms , insulation, and energy efficient LED lighting.
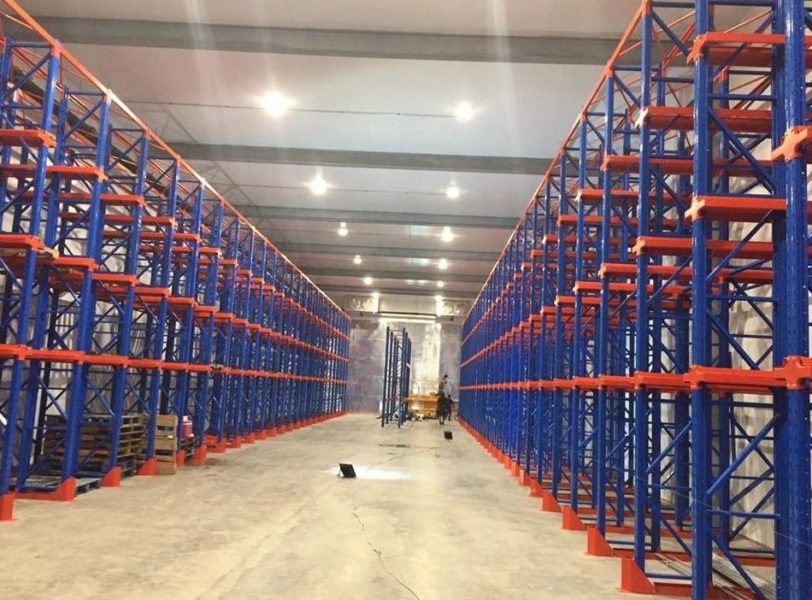
A supplier of commercial & industrial cold storage and refrigeration products, energy management systems, service & maintenance, design, and engineering.
Refrigeration
A typical refrigeration system comprises of a condenser, compressor evaporator, variable frequency drive and motor. All of these must be balanced with demand and ROI.
Refrigeration Controls
Automation also increases efficiency levels, while also optimizing energy consumption. Plus, engineers enjoy features such as data management, trend analyses and real time reports. This allows necessary changes to be made in a timely manner and ensuring that all systems are always performing at their maximum efficiency.
Electrical Utilities
Power loss can pose to be a huge problem from a financial aspect. Therefore, electrical design considerations should include operating voltages, supply reliability, standby generation and suitable locations of electrical rooms from where power is distributed optimally.
Roofing and Insulation
Cold storage warehouses must be equipped with proper insulation and seal panels. Floors, roof and walls should be of adequate thickness and must be coated with reflective materials that reflect the sun’s rays away.
Suspended Ceilings
Suspended ceilings must be set up at strategic positions, close to drainage points that can remove water buildups. The materials should be able to bear the load of the facility.
Structural Supports
The structure should be designed so as to ensure that none of the columns or supports hinder nay operational activities.
Airflow
Evaporators must be installed at suitable positions such that airflow can be reduced and snow formation can be limited. Refrigeration fans that don’t operate in presence of personal are a preferable feature and so are rapid roller doors that maintain a warm space for employees and chilled environment for the products.
Flooring Systems
The floor should be made from concrete, properly leveled and fee of cracks. Moreover, it should be post tensioned so expansion joints are not needed. Vapor barriers or sub floor heating systems may be used for maintaining required insulation.
Amenities
Cold storage facilities should be designed to maximize the storage space as well as the number of employees. Various amenities should be offered to them so that they can work comfortably, delivering higher productivity levels.
The Constructors
Many companies will readily build a cold storage facility for you, but before bringing them on board, ensure that they are a good choice. Try to hire a company that has experience, has already completed a similar project like yours, and has an idea of potential challenges that may arise during planning and execution. Be informed by talking to industry experts, ask for recommendations, read online reviews, attend tradeshows and then narrow down the names you come across.
Understanding Factors that Affect Cost
Integration of Key Systems
Cold storage warehouses don’t only comprise of freezers; there are so many other components which must be integrated seamlessly with proper functioning.
HVAC System
Cold air is generated through an anhydrous ammonia unit. Considering costs of these refrigerants, the following points should be kept in mind, all of which incur greater costs.
- Ammonia isn’t compatible with copper pipes, meaning that you’d require another suitable material which may add to the overall costs.
- Also ammonia is harmful to humans. Thereby, all personnel on duty will require extra training.
- Deploying essential security measures and providers workers with necessary safety equipment and gear are also mandatory.
Insulation
Cold storage must be maintained within a certain range of temperature, which is only possible through robust insulation. Care must be exhibited when installing, ensuring that entire warehouse is sealed tightly. If there are leakages, the result will be an increasing load on the cooling units and impacting power bills. This also subjects HVAC systems to the risks of breaking down, another concern that must be dealt with.
Insulation can be achieved through several materials, but of course, the overall efficiency and R values vary. Fiberglass is an economical option, whereas polyurethane foams are expensive. Temperature transfer resistance depends on the R value; higher values do imply greater upfront costs, but they also improve insulation, contributing to costs savings in the long run.
Another consideration is the flammability of some insulation types and the harm they can exhibit on the environment. Often cold storage warehouses are constructed using multiple insulation materials to balance R value, e environmental impacts, fire risks and costs.
Here is a rundown of some common insulation materials.
Material | Price per Square Feet | R Value per Inch | Environmental
Concerns |
Flammability | Key Properties |
Fiberglass | Low | 3.1 | No | No | Doesn’t absorb water |
Mineral wool | Moderate | 3.1 | No | No | Doesn’t support combustion and doesn’t melt |
Cellulose | Moderate | 3.7 | No | Yes | Contains recycled content in the greater quantities |
Polyurethane foam | High | 6.3 | Yes | Yes | Offers good sound insulation |
Polystyrene (EPS) | Low | 4 | Yes | Yes | Is utilized with difficulty in case of imperfections |
Fiberglass
Fiberglass is probably the most common material used for insulation, capable of minimizing heat transfers because of its weave of fine glass pieces and an insulative material. But, fiberglass does expose personnel to risks when being handled. Since it is made from woven silicon and glass powder, tiny glass shards are formed that can damage eye, lungs and skin if necessary safety measures aren’t taken. Nonetheless, fiberglass offers good insulation and isn’t flammable. R values fall between 2.9 to 3.8 per inch, and prices are within an affordable range.
Mineral Wool
The term, mineral wool, refers to different insulation types such as glass wool, rock and slag wool. Glass wool is actually fiberglass that is made using recycled glass. Rock wool is produced using basalt. Slag wool comprises of steel produced at steel mills.
Mineral wool doesn’t offer much resistance to fire, and hence, it shouldn’t be used in situations where generated heat levels are high. However, the material is still not combustible. When used with other inflammable insulation materials, mineral wool can still be effective. R values range from 2.8 to 3.5.
Cellulose
Cellulose is available in a lose form, made from paper, recycled cardboard and other materials. R values are between 3.1 and 3.7, which is good enough for most applications. Cellulose minimizes potential damages due to fire; it has a compact nature, doesn’t contain any oxygen, and so doesn’t contribute to fire. Cellulose is available at economical rates, but sometimes, it may cause allergies.
Polyurethane Foam
This material offers excellent insulative properties, but not used where costs are too much of a concern. Polyurethane foam is expensive, but nonetheless, a worthy investment. Polyurethane is light weight and has an R value of 6.3. The low density makes it possible to spray the material into areas where no insulation is present.
Polystyrene
Polystyrene is thermoplastic foam of a waterproof nature. It offers a resistance, not only to heat transfer, but to sound as well. Polystyrene comes in two main types: expanded and extruded. The former is abbreviated as EPS and the latter is referred to as XEPS or Styrofoam. The R value of EPS is 4, whereas for XEPS, it is 5.5. The surface of both these materials is smooth, a feature no other insulator possesses.
Generally, polystyrene is used for making blocks which are used for insulating walls. The material is flammable, and must be coated with a fireproofing substance prior to installation.
Other Choices
Other insulators can also be used, but they are preferred in limited applications. Pyrogel is used in industries where efficiency is a concern. Natural fibers like cotton and sheep wool are also common choices.
Power Supply and Backup
Cold storage warehouse consumes power in significant quantities, most of which is utilized by lighting and the HVAC systems. Other components may also require power such as automatic doors, response systems and security monitors. All this adds to operational costs, which can rise rapidly if specific guidelines aren’t adhered to. Moreover, another power supply source should be consistently available as an alternative, which increases costs even further. Even at a bare minimum, this backup power should be sufficient enough to maintain the required temperatures so that perishable goods aren’t ruined.
Materials
Different materials and methods can be utilized for constructing cold storage warehouse costs, depending on the goals of the projects. On some of these, the requirements are absolutely clear right from the start. Owners know exactly what they want from the building materials right down to the diameter of the drains. Considering other projects, stakeholders lay out their requirements, and then turn to their construction consultants for layout design.
Many a times, cold storage warehouses are often taller than other general storage units so as to store greater quantities of goods within a given area. When estimating material costs, the following points must be considered.
- The concrete used on the floor and for the foundation should be strenuous enough to handle the relative square footage load. For floor heating systems, greater quantities of concrete are needed which increases costs. But they are preferable because they dry up the floor quickly, and thus, prevent bacterial growth.
- The structure should be customizable to at least a certain degree. Often, the tilt-up construction method is used because it’s easy to build panels of the required size using local ready-mix rather than using custom fabricated steel from an outsourcer. Moreover, the former option requires less labor, another cost-impacting factor.
- Tilt-up concrete is a good insulator. Multiple layers of the same material do improve insulative properties, but at a price. But as already stated, it’s better to spend more upfront than incur costs later on.
Energy Saving Elements
Energy saving elements may be a bit more expensive, but they do reduce operational costs. LED lighting, automated mechanical systems and similar components provide greater ROIs and increase efficiency levels. Refrigeration systems and compressors can also increase efficiency, and thereby, reduce costs.
Delving into the Figures
The total costs of building cold storage warehouses can be broken down into three categories: building construction, unit construction and equipment costs. For estimating prices of the ventilation systems, all the prices of sub components should be evaluated to reach a total figure. It’s important to consider other relevant information as well. For instance, evaporative cooling pads may wear out with time, and have to be replaced. They also require water pumps for maintaining moisture levels. Both these increase operational and maintenance costs.
Temperature and humidity sensors would be installed in all rooms such that they can adjust the airflow. As for lumber, prices widely depend on the size and quantity.
Electricity Costs
Electricity costs roughly come out to be $2,300 per year for air conditioning and fans. 10% of this is for miscellaneous equipment and needs. Temperatures are warmer in summers, which ultimately, lead to greater bills. From August onwards, the monthly costs operational costs fall down as lesser energy is consumed.
Roughly, the average monthly bills for the period between June and July are close to $450. In August, they decrease down to a little bit over $150. From September till February, average monthly bills remain within $100.
Comparing Costs of Cold Storage Units Located Above the Ground and Below
A typical above ground unit is based on modular construction featuring fabricated metal panels with an R value of 34. HVAC units are installed inside, often situated near a metal pole barn so as to save on insulation, concrete and lumber. Electrical costs will also rise because of increased heat conduction gain. Total costs of such a unit are around $33,300, whereas a basement unit incurs upfront costs greater than $50,000.
Dealing with Potential Risks
Cold storage construction projects do exhibit certain risks which add into the cost. These are given below.
- Food safety risks – contamination, bacterial growth
- Worker Safety – Slip hazards
- Increased bills – air leakages, poor insulation
- Aesthetic damage – staining due to moisture
Keeping Your Budget under Control
Construction costs of a cold storage facility can rise exponentially, and the best way to control them is strong planning right from Day 1 of the project. During the planning and design phase, the entire team should sit down together and assess needs of the facility. Accordingly, they should develop a realistic budget and schedule.
Identify the design, layout and performance criteria, and then seek bids from subcontractors. Any changes made after this will further affect costs even if they seem minute. Once the plan has been finalized, and construction begins, ensure that the project remains on schedule throughout. This is one of the best ways to stick to the budget.
Cold storage construction is a mega project and a heavy investment, but can be closed successfully if built and executed upon a strong plan and design.
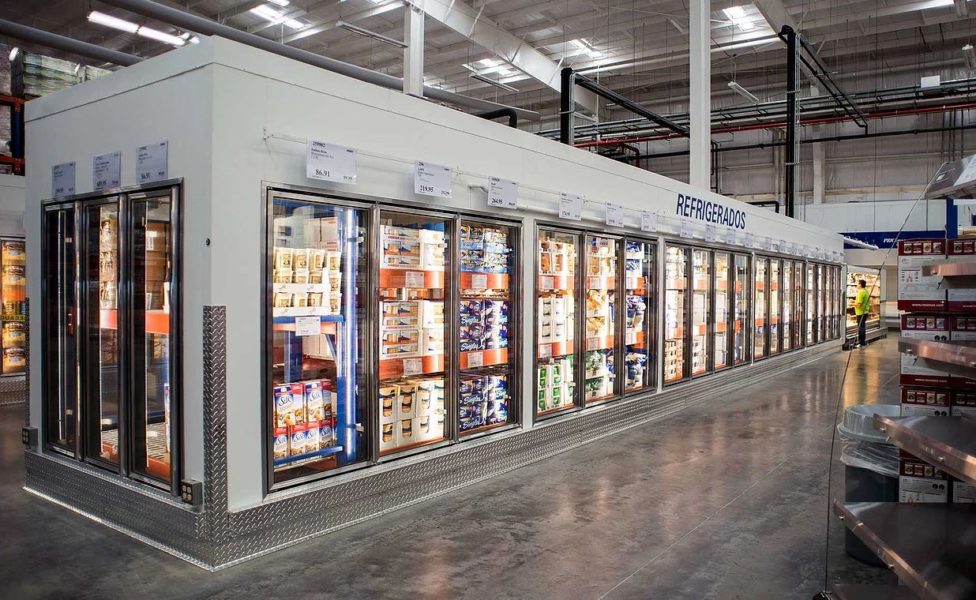
A supplier of commercial & industrial cold storage and refrigeration products, energy management systems, service & maintenance, design, and engineering.