There’s a good chance you’re already considering the construction of steel buildings if you’re reading this buyer’s guide. Maybe you own a small company and are in need of some extra storage room. You might even be on the lookout for a hangar to store your airplane, a stall to maintain some animals, or just an area to conduct your hobbies. The potential is endless. Fortunately, there are many possible variations when it comes to building steel projects.
Steel constructions are becoming the go-to solution for challenges of space that people face in the world today. You should take a second to think about why this is the case. Currently, steel buildings outrank other forms of construction when it comes to economics, flexibility, and aesthetics.
You’ve probably already conducted a little bit of research if this is your second visit to this page. Now that your opinions of steel buildings have become even more positive, it’s safe to assume that you’ve returned to learn about what goes into erecting one of these structures.
9 important things to consider when buying a steel building:
The Advantages of Using Steel Buildings
From saving money and ensuring the build quality of your new structure to finding solace in energy efficiency, there are several advantages to PEBs and reasons why you should consider using them.
The advantages of using steel buildings can be grouped in 4 categories:
Cost Reduction Advantages
Rapid Completion
PEBs are pre-engineered unlike some other forms of buildings. This means that your construction is going to arrive just a few steps away from a complete building. A standard DIY project can be finished in a matter of weeks with a steel building kit. For more traditional forms of construction, the completion time hovers around 1-6 months.
Lower Overall Cost
The overall assembly cost is much lower for PEBs than it is for other forms of traditional construction. The building parts necessary for steel buildings are all designed to fit perfectly together like puzzle pieces. Since they’re cut and prepped using an automated process, production costs go down. Overall cost of construction can be cut by nearly 60% when using these types of buildings.
DIY Construction
Constructing your own DIY building with steel parts can end up saving you half of overall costs. Since everything is pre-made, you cut out significant expenses that would go towards hiring laborers.
Construction Accuracy
Recent advancements in technology now make it possible to construct buildings more accurately. With each piece specifically cut to fit with the others, your PEB is going to fall into place much smoother than other buildings. This works to cut out preventable costs including excessive materials and labor.
Saving on Energy
This precision throughout the process also reduces the potential for gaps in windows, doors, and other areas where air might escape. When you throw in a reflective paint job, you get a real recipe for reducing HVAC costs.
Savings on Insurance
More traditional building styles made from wood typically incur higher insurance rates than their steel counterparts due to flammability issues. In fact, premiums for steel buildings can be nearly 40% less.
Reduction in Maintenance Costs
PEB buildings that use steel are built to last. Many come with paint finishes that include multiple-decade warranties that protect against peeling, blistering, cracking, chipping. Wooden structures are subject to potential warming or rotting while steel buildings aren’t.
Comparing Steel Costs Versus Those of Other Construction Types
Steel Costs Vs Other Construction Methods
Construction Method | Materials | Labor | Total Cost |
Stud Frame | $13-$23 | $15-$26 | $28-$48 |
Post Frame | $10-$19 | $12-$21 | $22-$39 |
Steel Frame | $7-$11 | $5-$9 | $12-$19 |
Safety Advantages
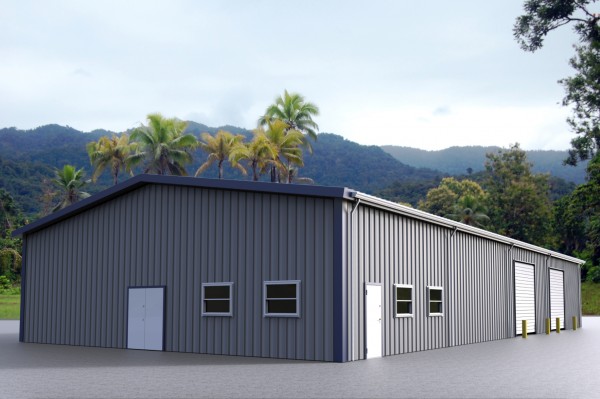
Enhanced Durability and Strength
Since steel buildings are constructed with solid components, they’re able to withstand some pretty harsh weather. In fact, many models are designed to handle winds traveling at speeds of 180 mph and loads of snow reaching 120 lbs/sq ft. Whether you’re in Alaska or Florida, these PEBs are ideal.
Stable and Secure
Metal buildings aren’t going to contract or expand as moisture levels fluctuate.
Reduction of Fire Risk
In addition to the reduction in insurance premiums, steel buildings also give owners an extra peace of mind that their structure doesn’t have a high likelihood of catching on fire.
Containment of Fire
If there is a fire, steel buildings are able to trap the flames to prevent the spread of the problem. This is due to the inherent properties of steel that are flame retardant.
Environmental Advantages
Recyclable
Steel buildings can be recycled and are also often called ‘green buildings’ since they use fewer materials, less energy, and develop less waste when compared to other construction methods.
Friendly to the Environment
Steel buildings only require around six scrapped vehicles for construction while a normal home with 2,000-square-feet needs around 40-50 trees. -The Steel Recycling Institute
Reduction in Waste
Buildings built with prefabricated materials are typically producing less waste than those that utilize traditional methods. When there’s no need for prepping, drilling, or cutting on-site, the amount of material waste produced is greatly minimized.
Not as Toxic
Steel buildings can last longer than more traditional, wooden structures that require the use of harmful chemicals to prevent natural processes such as rotting. The environment isn’t the only benefactor of this difference. Any livestock you house in these steel structures also benefit from the lack of chemicals.
Flexibility
Expanding
Since PEBs are designed modularly, it’s quite easy to expand. Parts can be added cost-effectively and at a rapid pace. All you have to do is remove a piece and add another, like a puzzle.
Relocating
Buildings that are under 10,000-square-feet are able to be taken down and relocated with ease.
Boundless Design Possibilities
Architects can have a heyday with steel buildings with the sheer variety of architecture options. There are so many wall panels and roof panel choices that combine for an endless array of possibilities.
The Steel Building Construction Process
Planning is an integral part of all building projects, and the construction of steel buildings is no exception. Generally, projects tend to go smoother if there was sufficient planning beforehand. Let’s get a bird’s-eye view of the planning process necessary for constructing a PEB so that you can plan in confidence, more efficiently, and with safer investment.
The following are 10 important areas to consider in the steel building planning process:
- Planning
- Engineering
- Ordering
- Manufacturing
- Preparing
- Delivery
- Erection
- Construction
- Finishing
- Walkthrough
Planning
Large projects always start with a single idea. Beginning the planning process on a piece of scrap paper is a great way to get this idea to flourish. You can think about where you want the accessories such as windows and doors, how large the structure will be, and what it will be used for. Placing your thoughts from your head onto a piece of paper, or 3D building design platform, can really spur the creative process. When you finally talk with an engineer, you’ll have a good grasp of what you’re looking for in the final product. It’s also important to set a budget.
After you’ve generated the seed, it’s time to water that initial idea by making more choices. For example, you need to choose the style of construction you want, the place on your property where it’ll be built, the type and number of accessories you need, and much more. Putting those personal touches on your building is a fun part of the overall process. However, you don’t have to rush into it. You can always make changes throughout the process, after consulting with the professionals involved.
At this point, it must also be decided if general contractors and erectors will be hired or if you’ll handle some of the processes on your own, DIY. There’s no right or wrong answer to these questions as it’s all up to personal preference and capability levels.
Engineering
Once you’ve completed the first steps, you can start consulting with the professionals about the engineering of the design. The vast majority of manufacturers keep engineers on staff. These professionals will transform your sketches and ideas from mere abstractions into an actual design. The overall price of the project will be greatly reduced since only pre-engineered parts are being used. Regardless, you’ll be left with a product that was inspired by your specific ideas and needs. The manufacturer will also make sure the construction is compliant with your area’s building codes along with other requirements.
Ordering
After deciding on a particular manufacturer to finalize your design and receiving all necessary approval from local authorities, you’ll be required to place a deposit and an order before any real work can begin. This is standard procedure for most professionals to ensure that they don’t invest valuable resources before receiving a commitment from the client.
Once the drawings are all made up, you might receive erection diagrams and plans for the building. This gives you plenty of time and information to prep the building site before manufacturers break ground. Some professionals might even opt to send anchor bolts that will be used to secure your building to the foundation. These can be used to prepare and lay the foundation as other parts of the construction are manufactured.
Manufacturing
As you prep the construction area for installation, your manufacturer is going to be kept busy making each component of the building. Some pieces might even be taken from inventory if they’re more standard than other customized parts. Unless you plan to erect the building on your own, you’ll need to scout out a general contractor and erector to help. Once the components are brought to your property, everything should be ready to go.
Preparing
Some merchants offer site preparation as part of their overall package, but most manufacturers require that the buyer prepare the construction site. While the manufacturer is busy producing the individual components of the PEB, you’ll need to prepare the site for the erection of the building. Grading, brush removal, excavation, and surveying are just a few components involved in this process.
The foundation engineer will design the details for the size and type of foundation needed for the building to function properly. Although poured concrete is the most typical foundation, there are other types that can be used with regard to the intended use, climate, and location.
Delivery
Be sure to cooperate with your general contractor or erector when it comes to the delivery. You’ll hold responsibility for receiving the order, and the contractor needs to be there to ensure that everything you purchased has arrived, confirming the inventory. All damaged materials and shortages need to be noted and reported to the building supplier. You are typically allowed 30 days to complete the inventory check-in. Cover up and protect the building materials if the construction process isn’t going to start right away. Make sure to follow the manufacturer’s steel building installation manual.
Erection
When you hire a general contractor or erector to handle the assembly of your building, it’s tempting to take a back seat and watch the process from afar. However, it’s important to be present for consultation if any questions come about naturally. The process of erecting steel buildings usually includes setting up the columns, placing the girts and purlins in the right place, and attaching the roof and wall sheeting. Make sure you have all contracts and paperwork handy just in case there is any confusion about what the general contractor is responsible for.
If you’ve decided to tackle the erection process on your own, DIY, be sure to follow the instructions carefully. The same goes for safety instructions. Like any form of construction, serious injuries can result from poor handling or improper techniques. Doing everything right is going to make it easier to enjoy your construction and will lower your costs overall. Make sure to do enough research on the construction process before venturing into that territory on your own.
Construction
After all of the erecting has been accomplished, you’ll be left with the building shell. If you decide to do so, It’s now time to fill out the building. You’ll either hire a contractor or do it yourself to add interior ceilings and walls, skylights, windows, doors, HVAC and electrical systems, insulation, and rough plumbing. Or leave the materials exposed and enjoy the industrial look and feel of your new building.
Finishing
If you chose to do so, in order to complete your structure, you can lay down flooring, paint ceilings and walls, and install external lighting and plumbing fixtures. The outside of the building will need door and window trim, decking or steps, downspouts and gutters, and any other external adornments you’ve decided on.
Walkthrough
While it all depends on where you live, there’s a chance that the new construction will need to pass various phases of inspections. These inspections will be required at intervals in the building process before anything continues. Once the building is completed, you’ll have to book a final inspection with a professional inspector that deems the construction up to code. The inspector will usually issue what’s called a Certificate of Occupancy to give you permission to use the building. You’ll probably do a personal walkthrough of the construction with your contractor in order to make sure everything meets your needs. You can make a short list of small corrections that need to be made in order to schedule the necessary appointments.
We sincerely hope that this short overview gave you some peace of mind and useful information. It’s very exciting and rewarding to design, build, and own your very own Pre-engineered metal building.
Planning
Lets explore some planning tips for anyone who’s thinking about replacing their existing construction or building something entirely new from pre-engineered steel.
Before, we covered various stages in the planning process. Here, we’ll dive deeper into the planning stage by looking at both practical and legal factors that should be taken into consideration.
Practical Factors
Everyone needs to think about how they’ll use their new construction. For instance, a building being used as a warehouse will probably need high garage-like doors for larger vehicles to get through. All steel buildings need strong foundations. In most cases, concrete slabs are the perfect solution. However, there are times when alternative options will be more practical.
You’ll also have to think about the following when it comes to choosing a location for your building:
- Drainage capabilities
- Accessibility
- Level and firm ground
- Nearby utilities
- Space for future expansion
Legal Factors
Your project will be subject to the building codes unique to your state. These codes dictate everything from the use of the building to construction requirements. It’s important to consult your local planning department prior to beginning because these codes are always subject to change. Anyone building a garage for emergency vehicles or a church might be subject to “important “factors” which raise these standards even higher than normal requirements.
Energy codes, drainage requirements, and zoning laws are some other examples of legal requirements you could be subject to. Some states enforce strict energy codes that require the implementation of “green” standards which work to reduce the carbon footprint of the construction. Using more insulation to conserve energy is one possible example. Although it’s a little bit more expensive at first, these insulation requirements are going to increase the energy-efficiency of your building over time. It might even end up paying for itself within the first year due to the reduction in cooling and heating costs.
Many parts of your building design will include both legal and practical considerations. For instance, retail facilities will have to, both practically and legally, offer parking with handicapped access.
Although some suppliers of steel buildings will help guide you through these complex building codes, most won’t even ship, fabricate, or even engineer buildings that aren’t compliant with the relevant requirements in your area. At the end of the day, it’s up to you to become familiar with these codes. If you don’t have experience in this area, don’t be afraid to talk directly with local contractors. The one who is the most helpful could even be brought on board as your erecting contractor when the building needs to go up. It can’t hurt to start talking with one.
Physical Building Factors
Building Orientation
The amount of sun and wind exposure your building gets each day might be an important factor to consider, although it all depends on your intended use. Will you want to design the building so that sunlight is pouring in throughout the day? Do you want to refrain from using doors and windows on one side of the building where the wind would be relentless? Maybe there’s an awesome view which you want to take advantage of. Those are just a few questions that you’ll want to think about when building.
Building Dimensions and Overall Size
It’s typically recommended that buyers of pre-engineered metal buildings opt for something bigger than their initial estimates. This suggestion derives from the natural process of growth. That way, you don’t have to spend money on additional space immediately after construction when your operation grows. It’s advisable to choose a size larger than you might initially think. Typically, dimensions for pre-built constructions are counted in 10s. For example, 40 feet x 50 feet or 50’ x 100’. However, you can get custom dimensions with minimal impact to the cost. 60×120, 50×100, 60×40, and 30×40 represent some of the more common sizes for steel buildings.
Building Height
The height of multi-story and single-story buildings are typically determined by local codes. However, those of community buildings will vary depending on the needs. Generally, a building’s eave height has to be a minimum of 2 feet higher in comparison to the tallest framed opening.
You’ll be able to determine the height of your building’s roof by the style and type of construction. For instance, aircraft hangars must use the high clearance offered by the clear span roof style. In order to achieve a feeling of spaciousness, churches might opt for high vaulted roofs. Normal roof height is typically sufficient for most office buildings.
Roof Pitch
A roof’s shape can be determined by the amount of space needed in the center of the room. The slope of a roof is represented through what’s known as the “roof pitch ratio”. This is expressed by the measure of rise for every foot of length. There is a colon in between these two measurements. For instance, a roof pitch of 1:12 or “one-in-twelve” has a slope that goes up two inches with every foot of horizontal length.
A 1:12 roof pitch is standard for most metal buildings and is nearly flat all the way across. 4:12 is normally the pitch measurement for gable-style buildings. A lot of space can be obtained for a little bit more money through the use of high-pitched roofs. If the extra space can be utilized, then the extra investment is definitely worth it. However, roofs with lower pitches have the advantage of being easier to cool and heat more easily. Depending on where you live, a roof pitch that’s steeper could be an added advantage because it sheds snow much easier than roofs with shallower slopes.
Framed Openings
A building that has any opening larger than the typical door frame has what’s known as a “framed opening.” These openings are typically very large so that big pieces of equipment, massive vehicles, and large stockpiles can fit through. A standard garage doorway is known as a framed opening. Factories, retail stores, and schools might also have a framed opening that’s used as a loading and unloading area.
Designs
Once you’re familiar with the advantages that a steel building offers, it’s time to find the best design to fit your needs. Typically, DIY prefabricated metal building kits come in one of two different designs. These two designs are then normally divided into two subcategories. Next, we’ll take a look at these designs, their differences, and unique features to give you a better idea of what you’ll need.
Quonset Hut
Although the name might be unfamiliar, one look at these lightweight, versatile structures will be sure to ring some bells. They’re good for easy transportation and quick assembly without the need for large teams of skilled laborers. The half-dome style gives the structure a lot of durability and strength. Despite its relatively affordable price when compared to many other types of steel buildings, the Quonset Hut is able to withstand seismic conditions and strong winds. These structures are also revered for their long-lasting qualities. With the proper setup and basic maintenance, a Quonset Hut could last for decades.
Rigid Frame
Generally speaking, aesthetics is the primary advantage that Rigid Frame buildings have when compared with the Quonset huts. Rigid Frames structures look like more traditional buildings. Although being slightly more expensive than Quonset huts, Rigid Frames are still more affordable than other steel building options. They’re also known for their dependability and sturdiness.
As with all PEB styles, the specific design chosen will be determined by your intended use for the building. Let’s explore some various Rigid Frame styles from which you can choose.
Straight Column
Systems with a straight column design are economical options that offer spacious interiors that reach nearly 70-feet in width. They are often used for commercial applications such as retail stores, offices, small gyms, and more.
Beam and Column
These Rigid Frame systems are often used to make spacious buildings that have vast floor space. Despite their affordable price, these structures make it easy to expand in the future. Beam and Column PEBs are perfect for industrial and warehouse purposes.
Lean-To
If you’re hoping to achieve expansion without spending much money or investing much time, lean-to structures are your best bet. You don’t have to interrupt any ongoing operations as these ‘wings’ can be set up economically, quickly, and easily. They’re great for use in a variety of applications including equipment storage, product storage, and loading space.
Open Web Truss
When structures are in need of longer spans, open web truss-style buildings can offer fantastic flexibility when it comes to design options. These framing systems are strong, light-weight, and ideal for areas where clear floor space is required, such as for indoor stadiums or aircraft hangars. The vast clear spans offered by these structures make their design quite versatile.
Clear Span
Clearspan designs take advantage of rafters and tapered columns in combination with girts to offer optimized span capabilities without obstruction. Column-free and clear-spanned structures offer vast interior space that’s not obstructed by anything. These sturdy designs are great for larger commercial buildings, aircraft hangars, auditoriums, gymnasiums, and other recreational applications.
Multi-Span
Multi-span designs share many features with clear-span structures. However, an interior column is added in order to allow the building to attain an even greater width. These designs are economical and are great for commercial, warehouse, office, and industrial uses where some columns on the interior wouldn’t obstruct organizational processes.
Terminology for Metal Buildings
The terminology involved with metal buildings evolves over time as new technology is developed both in terms of production and design. Are they metal buildings, pre-engineered buildings, prefabricated buildings, modular buildings, structural steel buildings, or something else completely? Although all of these terms are encompassed under the term ‘metal buildings’, each one points to some slight variations in design, production, and function. Let’s dive into each term to give a better idea of what they’re referring to.
Modular Buildings:
Modular buildings are sent to the construction site in various building segments that are three-dimensional. They’re produced and designed in manufacturing facilities and sent in various forms. You can receive modules that are semi-finished and fixed once at the construction site. You can also opt to receive ‘building blocks’ that are essentially completed sections of the building.
Prefabricated Buildings:
Also known as prefab buildings, these PEB styles are designed, created, and assembled offsite. Although early versions of metal buildings built between 1850 and 1960 were appropriately called prefabricated buildings, the term Metal Building Systems is more apt name for modern versions of the prefab building. These modern versions are finished at the factory. Classrooms, guardhouses, and toll booths are just a few examples.
Pre-Engineered Buildings:
This style of building got its start in the early 1960s. They were originally given the ‘pre-engineered’ name because they were made from designs already at the facility that were standard at the time. Customers could select from a variety of standard dimensions of a steel building such as 60×100, 40×80, 40×60, 30×50, 30×40, etc. These designs typically came with standard dimensions and framed openings that would be used for windows, doors, loading areas, and more.
Metal Building Systems:
Metal Building Systems encompass all of the modern buildings you see today that have basic exterior finishes, roof or wall panels, and roofs with low pitches. Distribution centers and residential garages are a few examples. This exact term has been adopted by the official industry to better describe the types of structures being produced.
Metal Building Accessories
Accessories for pre-engineered buildings are all things that aren’t the roof, structure, or foundation. It’s helpful to think of these options as customizing features. We’re going to take a look at some of the various options here. Keep in mind that this is not a complete list by any means. When you get to work on your own building, you’ll find many other potential options that will make it easier to customize your structure and make it fit in with any existing buildings, if that is what you wish to do.
Framed Openings for Doors
Framed openings are sometimes left in PEBs to enhance customization. Doors are a typical accessory that ends up filling these openings. For larger openings, a sliding door is one example of a possible option. Overhead doors that are automated and mechanized can be especially convenient for some applications. Aircraft hangars, storage buildings, and warehouse applications are just a few examples.
Walk-Doors
The vast majority of metal buildings need doors in order for people to walk in and out of the structure. Typically, there doesn’t have to be any special framing around these walk-doors due to their small size. This is known as self-framing and makes it much easier to customize their exact location. You don’t have to take walk-doors into consideration when identifying the exact number of openings you’ll need in the building. When choosing which type of walk-doors you want, options with half-glass designs might be a good option to allow some natural light in.
Windows
PEBs may need windows to allow for sufficient ventilation and light. They also help to add a feeling of atmosphere and ambiance. Similar to walk-doors, windows in these building systems are field-located and self-framing. This means that they can be placed anywhere as long as there is no blockage from a column, girt or bracing. Most manufacturers will offer un-insulated and insulated, or thermal, models in a vast range of sizes. Thermal windows are the best choice for those planning to keep their structure climate controlled.
Skylights
If you’re looking for a way to flood your structure with natural light throughout the day, skylights are a great option. These accessories can also work to boost your structure’s energy efficiency. When constructing metal buildings, manufacturers will simply substitute a standard roofing panel for something translucent. Polycarbonate panels can be used when durability and strength are key. However, translucent fiberglass panels will end up being the most affordable.
There are some manufacturers that refer to skylights as “roof lights”. “Wall lights” are also an option offered when wall panels are replaced instead of roof panels. Skylights are typically added in pairs since one is installed on either side of a roof’s peak. Manufacturers will normally reference the number of spaces in between columns in order to determine how many skylights a structure needs.
Vents
Proper ventilation works to improve a building’s energy efficiency, makes it easier to heat and cool the structure, helps to ensure the air is always fresh, and reduces the amount of condensation, which is an important consideration for steel buildings. In order to ensure there’s enough ventilation within the structure, it’s important to have more than one device for the purpose of ventilation. Moving air in between these two devices is called cross-ventilation.
Turbine, gravity, ridge, and wall vents are all examples of typical ventilation system components. There are certain formulas that manufacturers will use in order to determine the right amount of ventilation for the function, structure, and size of your structure. They should also be more than happy to help you in choosing the best combination of ventilation devices given your particular situation.
Finishes
Most manufacturers offer their buyers a wide range of colors when it comes to roof panels, wall panels, and trim lines that go around the building. Many also make panels that have concrete-style finishes or acrylic stucco.
It’s also an option to finish and paint the building yourself. However, you’ll get a warranty when you purchase finishes directly from the manufacturer. Warranties for finishes and paint jobs can last anywhere from a few years to a few decades. It all depends on the company and the quality of the materials used. Panels that remain unpainted but have a coating of zinc-aluminum are normally warranted for two decades.
If you prefer to have your steel structure look more like a typical wood-framed building, you can opt for masonry, wainscoting, brickwork, stucco or wood paneling. Most people wouldn’t be able to tell the difference with a professional finish. For those who prefer to add their own finish with aftermarket products, general contractors can be hired to do this work.
Downspouts and Gutters
It’s easier to keep your building clear of any runoff when you use the right gutters. These accessories help to prevent pools of water from building in front of your door or in the parking area. In addition to having practical uses, downspouts and gutters add to the overall aesthetics of your building as well. In smaller buildings, they might also be used as the only ventilation device.
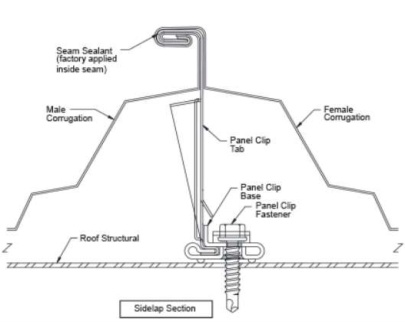
Standing Seam Roof
A standing seam metal roof system from Allied Steel Buildings is one of the most durable and weathertight roof systems available in the industry. There is less maintenance required throughout the life of your standing seam roof, and a minimum number of exposed fasteners for a unique aesthetic effect.
⦁ Can save up to 90% on roof maintenance costs
⦁ Better protection against severe weather, eliminating risks of leaks
⦁ Available in a variety of highly efficient Cool Colors
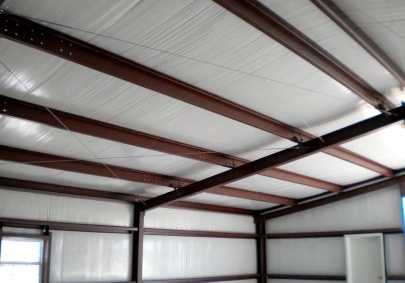
Insulation Systems
Allied Steel Buildings offers a wide range of insulation solutions designed to maximize and capitalize on the thermal benefits of your building.
⦁ Control heat flow reduces energy consumption
⦁ Protects against condensation
⦁ Reduces exterior sound and absorbs interior sounds
⦁ Increase lighting efficiency
⦁ Provides thermal barrier
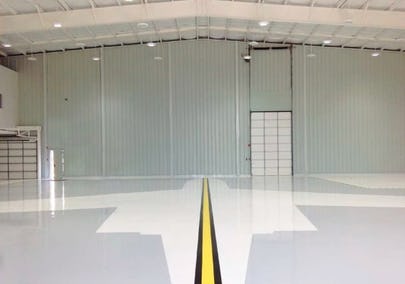
Interior Liner Panel
Interior liner panel systems mask the secondary framing of your building and provide a workable wall surface. Interior liner panels are available in 29, 26 and 24 gauge steel with multiple profile options.
⦁ Improves interior finish
⦁ Protect insulation from being punctured
⦁ Available in partial or full height
⦁ Available in a variety of colors
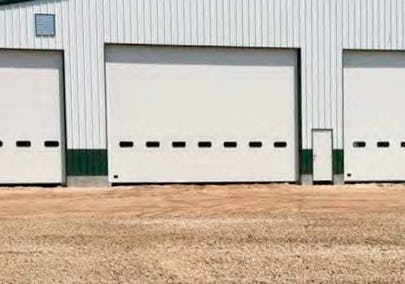
Overhead Doors
By choosing a commercial overhead door you are enhancing your building’s security and appearance. You can select from a variety of design options and colors that best suit your requirements.
⦁ Thermally broken insulated doors
⦁ R-values range from 7.5 to 17.05
⦁ Ideal for commercial and industrial applications
Pre-Construction Work
The construction of steel or metal buildings doesn’t differ much from the construction of other buildings. Everything begins with a sturdy foundation.
Before pouring the foundation, your contractor will have to ensure the land on site has been surveyed by a professional to make sure its level. The steel building manufacturers must also be aware of the plot’s dimensions.
When the site is marked and surveyed, the physical leveling or grading process can be started. This part of the pre-construction work involves morphing the shape and height of the land to meet the needs of the building.
After the entire site has been leveled per the requirements of the surveyor, you can start excavating to pour the foundation. It’s best to speak with a foundation engineer to determine what excavation type will be required. Many metal structures with simple designs only need a minor amount of excavation, however, more complex models require something deeper. Your building supplier will provide you with the building reactions that the foundation engineer can use to design the appropriate foundation.
Steel rakes, shovels, pickaxes, and other simple tools can be used for shallow excavation. Bobcat shovels, backhoes, and other larger pieces of equipment will be needed for major excavation needs.
Don’t forget to hold onto some of the excavated dirt. It might come in handy in the near future for leveling the building or final grading. You might also need some of that earth for in-filling and back filling once the construction is complete.
Federal Regulations and Rules
Departments of Consumer Affairs on the state level, the Occupational Safety and Health Administration, and other governmental organizations lay out strict requirements when it comes to pouring concrete slabs.
Following these strict rules will make sure that your building is built soundly and that it is legal.
There are also beneficial safety guidelines laid out by these departments for any laborers that are involved in the process of laying down concrete foundations. Always make sure the workers are protected and safe during this process.
4 Typical Kinds of Foundations
Slab
Slab foundations consist of poured and reinforced concrete. Both serve as the floor for the building and as the base to ensure a secure erection. Heavy bearing walls may have to be used around the entire perimeter of this slab and in other areas. If so, excavation must be a little deeper in order to provide the footings with stability. Slabs typically have a thickness of 3.5” – 5.5”.
Curb
Curb foundations only require reinforced concrete to be poured around the perimeter. Similar to street curbs, curb foundations stand a few inches above the grade and offer a secure base for the external walls of the structure.
Extra excavation can take place within the curb in order to offer a crawl space below the foundation if it’s within the owner’s preferences and if the land allows for it. Whenever extra curbs are created within the original curb to support weight-bearing walls, it’s called a “ribbon” foundation.
Floating Slab
Floating slabs are a combination of curb and slab foundations. They’re some of the most commonly used foundations in use today for a myriad of construction purposes. When the structure is being built on a relatively flat surface, a foundation curb with footings is going to be poured primarily. While that’s being set and cured, another slab is made within the perimeter of that curb. This functions as the ground floor for the structure overall. If done properly, floating slaps should help reduce cracking typically caused by settling.
Pier
Pier foundations give a building foundation through the use of individual piers (footings) which are set evenly throughout the perimeter of the structure. Typically, a pier such as this will be formed with reinforced concrete that’s been set deep below the ground to hit undisturbed dirt. Although they’re not recommended to be used for larger buildings, these pier foundations can be handy for smaller buildings like small shops or storage units. Speak with your engineer to hear about the individual pros and cons of using this type of foundation.
Mixing
Ingredients:
It’s important to choose the right ingredients when mixing concrete. This can determine the lifespan of your new structure. Concrete should always be durable and strong. Portland cement, gravel, sand, and water are the fundamental ingredients. Water retardant, fly ash, and other admixtures can be thrown in to help strengthen and cure the concrete.
Strength:
There are two ways to describe the strength of concrete. Tensile strength refers to the concrete’s ability to resist expansion or stretching. Reinforcing bars made from steel can be used to boost a concrete foundation’s tensile strength. The other measurement of strength is called compression strength. This is a measurement of the total time a concrete foundation takes to cure entirely.
Mix:
Concrete’s normal compression strength reaches 3,000 lbs. for every square inch within 28 days. In order to reach this ideal strength, the right mixture proportions have to be reached.
Forming
Forms have to be built before any concrete gets poured. Just like other forms used in construction, the concrete gets held together in desired shapes until drying completely. Forms are typically constructed from 2x4s although some people prefer using metal. It only matters that the forms are rigid and strong enough to not budge from the pressure that drying cement produces. Any deflecting, bending, or deforming is bad.
Pouring
Concrete has to be spread evenly to ensure that any aggregates don’t settle at the bottom. The concrete mixture must always be kept spinning to keep it from hardening. Double-check to make sure all of the air bubbles and voids have been removed and that the rebar is covered completely. For larger projects, some people opt to use a pneumatic or electric vibrator to guarantee that all air is taken out of the cement before it’s poured.
If you have to pour a deep foundation, keep in mind that water will sometimes rise to the top because of the pressure caused by gravel and sand. Latinate is the name used for this bleed-water and it has to be taken away once it arrives at the surface.
Screeding
The process of removing excess concrete from the slab once it’s poured is known as screeding. Typically, you’ll end up pouring a little more concrete than the project requires. Once you’ve ensured that all of the necessary areas are filled, you’ll have to remove the excess concrete so you’re left with an even and flat surface. Large metal or wooden boards called screeds are taken across the top of every form. Two people are usually needed to perform this job. Excess cement just gets thrown down at the end of each form. It can be left to dry and simply removed during the cleanup process.
Finishing
There are usually two steps involved in the finishing process. Step number 1 is to use large metal or wooden tools known as floats to force bigger aggregates down deeper into the mixture. These float tools are pulled and pushed around until the surface is smooth and even. The concrete is still going to be pretty wet.
After the rising water has been evaporated and the mixture allowed to rest, the second portion of the finishing process can begin. This is accomplished with steel trowels. These tools are used to create an even smoother surface on top of the mixture. Metal rakes will be taken to the concrete slab if it will be used outside in order to prevent slipping when it gets wet.
Curing
The Portland cement and water produce a chemical reaction that helps to cure and dry the cement. Moisture and temperature also directly impact the durability and strength of the concrete. The ideal weather conditions for creating a perfect slab of concrete is around 50 or 90 degrees Fahrenheit. Once 72 hours pass, the concrete should be sturdy enough for further construction.
You’ll have to take extra precautions and prepare something unique if you’re pouring the concrete in an area that experiences cold weather regularly. The same is true for areas that experience very hot weather. Concrete foundations that don’t settle properly could lose up to half of their strength and cohesiveness over time.
Anatomy of Foundations
Footing and walls are the two primary components of which concrete foundations are comprised.
Footing
The footing of a foundation refers to the structural units that require extra reinforcement and excavation. The purpose of footings is to help distribute the structure’s overall weight to materials designed for bearing large loads.
Wall
Foundation walls are just concrete walls that have been poured to extend below and above the ground level. These walls are load-bearing to help serve as extra support for the columns and walls of the structure.
Load Distribution
While steel constructions don’t produce much vertical load, there are a lot of horizontal loads that need to be accounted for. This tends to force pressure and weight outwards. If the loads can’t be distributed properly during construction, structural failure can result in the framing or the foundation. Fortunately, there are a few common methods for distributing and resisting horizontal loads:
Tie Bars
The first strategy recommends connecting steel tie bars to anchor bolts. This helps connect the columns of the building together for an evenly distributed load. For instances when the building’s horizontal load isn’t so high, hairpin or spread ties could be used to put the load onto the rebar that was used when making the floor.
Enhance footing size
Through this method, the horizontal load is counteracted and any chance of the foundation shifting is prevented. While this solution is effective, it is also more expensive than the other choice.
Pouring the Floor in 5 Steps
Slab
The majority of building installations have a floor that’s created through the pouring of a concrete slab. This happens within the walls of the foundation. The slab can either be poured when the foundation walls are built or once they are finalized. To avoid cracking and add strength, reinforcing bars made of steel are sometimes used in the floor as well. Concrete that’s resistant to cracks and rebar should also be used for buildings where heavy vehicles or machinery will be used.
Vapor Barrier
Visqueen, or a polyethylene plastic sheet, should be laid down on top of the surface where the slab of concrete will be poured before any pouring actually beings. This helps to prevent any water vapors from getting into the floor and allows for a better curing process.
Thickness
Each floor’s thickness will be dependent upon the loads it will have to bear over time. Normally, the thickness of a slab is equal to that of a 2×6 or 2×4. However, there are some buildings that require even thicker dimensions. Some jurisdictions even have requirements when it comes to a floor’s load-bearing capabilities and thickness. It’s always important to check your area’s building codes before starting the process.
Joints
Many concrete joints have to be placed between concrete pours or between other construction components. Expansion joints are often placed in areas where normal contraction and expansion takes place. This helps the floor withstand some normal movement in the concrete. When the concrete is being cured, it might shrink a little bit. During this time, the expansion joints will help to keep the concrete floor from falling apart and cracking. In the future, the joints will do the same when temperatures fluctuate and the floor contracts and expands.
Waterproofing
When the curing process is underway, it’s advisable to use some waterproofing substance in order to prevent any further intrusion of moisture. The best type of application technique and substance to use will depend on what the building is used for.
Insulation
There are a number of important roles that insulation plays in steel buildings. In addition to offering resistance to pesky heat transfer, insulation works to reduce condensation buildup in the building and minimizes the amount of external noise audible from within. Spending a little more money on good insulation will save you lots of money in the long run if you plan on keeping the structure climate controlled.
R-Value
Before explaining the various kinds of insulation and the advantages of proper insulation, it’s critical to know what the R-Value stands for. In simple terms, R-Value is the measurement used to determine to what extent insulation prevents the transfer of heat. The lower R-Value rating, the less effective insulation is at reducing heat transfer.
Bear in mind that fiberglass blanket insulation isn’t the best choice for steel buildings. In reality, the best choice is going to be a combination of reflective and fiberglass insulation. For example, Solar Guard and eFoil is a good combination.
There’s no shortage of options when it comes to insulation material. Furthermore, new forms are being produced every year as energy savings and thermal resistance become hot topics in the green building community. The graph below shows the R-Values for some of the most popular forms of insulation for steel buildings.
Type of Insulation | R-Value |
Fibreglass Batts | 2.9 – 3.8 |
High-Performance Fibreglass Batts | 3.7 – 4.3 |
Cotton Batts | 3.0 – 3.7 |
Sprayed Polyurethane Foam | 5.6 – 6.2 |
Loose-fill Rockwool | 2.7 – 3.0 |
Insulation Types
Fiberglass Blanket
Fiberglass blanket insulation is the most popular form of insulation to be used in PEBs due to the material’s quick installation process and cheap price tag. There’s the added advantage of fire retardation and sound resistance. This type of insulation is usually provided with a vapor retarder and receives tests for fire safety, mold, moisture, and odor resistance.
Rigid
Rigid or foam board insulation works by keeping air trapped in single cells of specifically designed foam. This type of insulation costs more to install and manufacture when compared with fiberglass blanket options. Furthermore, rigid insulation loses the ability to insulate over time. The sound resistance offered by fiberglass blanket insulation is also nowhere to be found in the rigid insulation. However, this form of insulation is very thermally efficient and vapor retardant. It also offers a lot of versatility when it comes to changing the appearance to match your overall aesthetic preference of the structure.
Spray-on Cellulose
Spray-on cellulose insulation is perhaps the form with the least number of advantages. It’s essentially a paper product that has a few fire retardant capabilities. This product should always be applied by an experienced and skilled laborer. Although it can successfully absorb noise and comes at an affordable price, there are many reasons not to go with spray-on cellulose. It absorbs oils and moisture quite easily which can lead to the corrosion of various metals. It also develops a rough look due to its collection of dust.
Loose-fill
Loose-fill insulation is a combination of fiber pellets and loose fibers. Cavities are filled with this insulation through the use of specialized equipment. You’ll have to pay a little extra for loose-fill insulation, but you gain the advantage of having your structure prevent air leakage a bit better. It also works as an improved barrier to sound. This type of insulation is typically used in floors, attics, and walls through an application process that uses a dry-pack or moist-spray process.
Proper Insulation Advantages
Minimizing Condensation
Steel and metal buildings are quite susceptible to damage through too much condensation. Rusting and other common issues are a normal occurrence. With proper insulation, the negative side effects of too much condensation can be greatly reduced. Insulation acts as a barrier to the vapor that keeps the condensation from taking place right on the structure’s panels. Furthermore, concrete foundations that aren’t cured properly can exacerbate the problem of humidity. In reality, the proper installation of insulation is typically more important than the type being used.
Controlling Temperature
Selecting the proper type of insulation for your PEB can work to reduce the amount of energy consumed through the climate control systems. Furthermore, some states make it possible for owners to reduce the amount of taxes owed by being eligible for “green” tax incentives. Alone, a steel panel doesn’t offer any protection from external temperatures. This means that the internal temperature will always be subject to the outside weather unless the right insulation is chosen and installed properly. When chosen properly, you’ll have a structure that is comfortable throughout the year without spending too much money on climate control.
Additional Advantages of Proper Insulation
- Prevents bugs, birds, and rodents from building nests
- Very easy to install
- Provides a barrier to vapor
- Has a high R-Value
- Helps to prevent the growth of mold
Final Things to Consider
Facing
Facing is a term used to describe the side of the insulation that is facing the interior of the structure. It’s important to choose the right facing material if you’ve decided to leave it exposed. When this is the case, facing insulation isn’t just insulation. It’s also the inner wall and should be reinforced through the use of scrim layers. Nylon mesh or fiberglass added to the facing insulation helps to increase the inner wall’s durability and protects against scratches, dents, and, punctures. Roof facing insulation doesn’t experience the same vulnerability due to its location. However, there are also some “bird proof” additions that can be added to the facing insulation.
Keep in mind that the lighting within your structure will be greatly dependent upon the color of the facing insulation. Reflective or white facing, you’ll need fewer sources of light. However, darker atmospheres can also be achieved.
Linear Panels
Full-height and partial linear panels are options from most manufacturers. These work to boost the aesthetic appearance of the interior of the structure while also protecting the insulation. A general contractor could be hired for the purpose of adding walls as well. The facing’s durability is drastically increased when protected and covered.
Permeability
In order to reduce condensation transfer, it’s important to use insulation facing that has a low permeation rating. Plain vinyl isn’t considered robust enough to protect against harmful condensation with a rating of only 1.0. However, anything with a rating that’s less than 0.1 is going to be sufficient for protecting against condensation transfer.
Workability
There are certain kinds of insulation that can’t be installed or shipped during the colder parts of the year. It’s important to speak with your manufacturer to determine if the chosen materials are workable given your location and the time of year.
What to do When Delivery Day Arrives
You might find it impossible to resist the urge to jump around with excitement when delivery day arrives at last. After countless weeks of planning, prepping, designing, learning, and overcoming obstacles, your new PEB is about to arrive at your building site. What you’ve imagined in your head and drew on paper, is about to become a reality.
Before you allow your excitement to get the best of you, it’s important to take a few particular steps to ensure that the delivery process goes off without a hitch.
Planning Before Delivery
You should make arrangements for the general contractor or erector to be available on the day of delivery. He or she should be placed in charge of verifying that each piece is delivered and in good condition. If you haven’t hired anyone to aid you in the erection process, then you’ll be the one who must ensure that every piece is there and accounted for. Make a list of anything that’s missing or damaged and share it with your building supplier.
When using a general contractor, it’s important to clarify who is going to be in charge of the staging and the off-loading of all the materials. Remember that manufacturers rarely offer equipment or labor to get the pieces off the delivery truck when it pulls into your lot. Make sure to have all of this sorted out before delivery day. Pallet jacks, forklifts, cranes, and other major pieces of equipment might be necessary to complete the staging and unloading, so plan accordingly.
When it comes to laying out your pieces, be sure to consider staging and access. Properties that are flat and large should be easiest to handle. However, if your site is oddly shaped and small, you’ll have to be very considerate about how you unload and organize the pieces of your PEB. The route the truck will take in and out of the property is also another thing to think about.
Two Inspections
If you hired a contractor, you and him or her will conduct two different inspections. These are the unloading and unpacking inspections. With the delivery truck still on the property, you’ll conduct the first inspection. The second inspection can be done anytime after.
It’s clear that your PEB is going to arrive in several separate pieces. All of them will be wrapped, boxed, bagged, bundled, and protected in every which way. Dig around in your file drawer to find the inventory list provided by the manufacturer. It’s advisable to make a few extra copies.
Unloading Inspection
You’ll have to give each item a quick inspection as they’re unloaded from the truck. Use the main copy of the packing list throughout this process. For each item you find damaged or missing, make sure to mark it on the list. You’ll use this information to report directly to the carrier while the truck is still there. If you come across any damaged packaging, open it up to see if the contents are damaged as well. The shipment isn’t considered officially delivered until you conduct your unloading inspection, check every item, and provide the approval to the deliverer. This step ensures you get what you need without having to pay extra for replacements or deliveries.
Unpacking Inspection
You can finally start the unpacking process once all of the items have been unloaded, the driver has left, and you’ve finished your inspection. Get ready for an even more scrutinous inspection of the items that were delivered. Grab another copy of the inventory list and start checking off each item once again. Double-check that everything arrived and that it all arrived in the appropriate quantities. You have 30 days to report any more missing or damaged pieces to the building supplier after the unloading inspection.
You might feel as though this second inspection is redundant and time-consuming, but it’s incredibly important to ensure that all of your structure’s parts have arrived intact. Although most manufacturers use advanced technology to make sure that everything is cut perfectly, packaged well, and delivered without any damage, accidents do happen. You’ll be making your building process much easier if you make timely reports and claims.
Staging Materials in 5 Steps
You should try and place each component closest to the spot where they’ll be used as possible. You might need to use special equipment to move larger items; all lighter and smaller items should be movable by hand.
Similarly, all columns need to be unloaded close to their final positions near their corresponding anchor bolts. Columns could be set on top of the concrete foundation if wooden blocks are set underneath. To make them easier to lift, it’s smart to keep cables under heavier columns. End Walls can be set towards the side of the slab near their erection point.
In order to keep track of your hardware packages, it’s smart to put them all in one place. You can reduce travel time and improve access by setting all of these items in the middle of the foundation slab.
Be sure to keep girts and purlins away from other pieces. Storing them near sidewalls isn’t a bad idea. You should also keep sheet goods away from other materials since these items are one of the last you’ll be using during the building process. Make sure to add some slope underneath to ensure any condensation or precipitation drains off the panels. Any accessories can also be placed on the side since they’re also some of the last items that will be added once the overall construction is built.
You also want to have the safety of workers in mind when placing items around the lot. Make sure no one is at risk of falling due to the poor placement of an item. You might even have to grab some covers for the pieces depending on the impending weather. This ensures they’re dry and ready to go once construction can commence.
Assembly
You can finally start the exciting building process once everything is delivered on time and intact.
The assembly process might be outsourced to a contractor or erector depending on your capabilities and experience with construction. Each choice comes with some inherent advantages and disadvantages. Considering the pros and cons of each can make it easier to decide and might even convince you of choosing something you didn’t think about before.
Hiring a Contractor
Outside Perspective
One of the major benefits of hiring a contractor is being able to see the actual process getting done. You have an outside and unbiased perspective of the work being done. You won’t be pressured to cut corners or accidentally ignore small mistakes if you performed the assembly yourself. To help the process run as smoothly as possible, you should strive to understand the process overall. Feel free to visit the building of other PEBs in your local area to see how it’s done. Get familiar with the order that things are done in. You could even speak directly to the owner and contractor in charge of the construction. Don’t be afraid to ask questions and tips regarding your project. Watching a project before diving into your own can make the process much easier.
Limiting Liability
Contractors bring experience and expertise to the table, but there’s another major advantage of hiring these professionals to help build your PEB. Upon signing the contract, you’re essentially handing over some of the liability involved with construction over to the contractor. This offers many people extra peace of mind knowing that someone else is involved in the decision-making process.
Working By Yourself
Be Safe
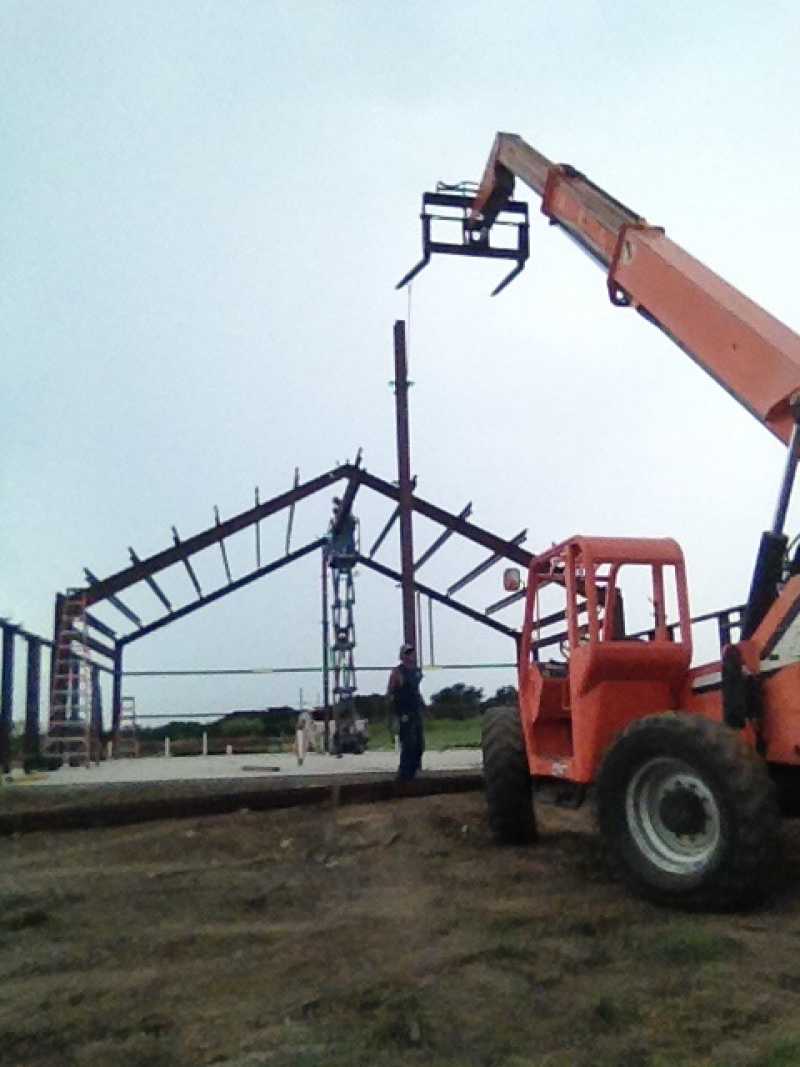
40×60 Steel Building Workshop located in Cleburne, TX
Safety should remain your top priority when entering into construction alone. All contractors have safety plans. Why should you be any different? Learn about the various hazards involved in the process including machinery, terrain, and climate. Be sure to dress appropriately and always wear protective gear when it’s necessary. Always ensure that hired laborers are also wearing protective gear. You’ll want to be mentally and physically strong each day as well.
Separate and Conquer
Many times, breaking down tough jobs into manageable chunks can make the overall process seem much easier. The same is true when it comes to constructing steel buildings. Think about each portion as its very own project. This will make it easier to stay focused. You might even be able to assign these separate jobs to teams, depending on the size of your workforce.
Hire professionals
Just because you don’t hire a contractor, that doesn’t mean that you can’t use professionals for certain portions of the construction process. Professionals will work safer and more quickly than anyone you could hire. You even save on instruction time since professionals already know what they’re doing.
Keep tools handy
There’s a good reason that professionals keep their tools with them at all times. It’s important to keep equipment handy to reduce traveling time and increase the speed at which your building is assembled. When it comes to larger pieces of equipment and tools, you need to make sure these are available for workers as well.
Don’t deviate from the plan
If you’ve done your due diligence when creating the construction plan, it should save you time and money if followed correctly. Don’t allow yourself to take any shortcuts in the process. When handling larger projects, you have to ensure that the entire process is mapped out and that every worker keeps a copy handy at all times.
Use bolts first
Before you raise any panel, be sure to bolt components together. Don’t cut any corners when it comes to safety, but piecing as many parts together as possible before lifting them can help save a lot of time.
Piece-by-piece
Construct in a natural, progressive manner. Be sure to assemble the framework of each bay before you move to the next.
Rent wisely
Unless you have access to equipment, you’ll have to rent most of it. You can save money by saving all work that doesn’t require the equipment until after it’s been returned.
Get enough sleep
Before leaving the worksite, take time to ensure that everything is safe and secure. Place tools in their designated spots, pick up all of the trash and debris, lock up any entrances, remove tripping hazards, and make sure that all drainage sources are ready to handle any water that may arrive on-site through the night.
You can maintain a safe working space, reduce building costs, and have a successful construction process by following some of these rules.